Segmentos da Área Química
Segmentos da Área Química
Na indústria de abrasivos, os profissionais da Química podem atuar na pesquisa e desenvolvimento de novos materiais, controle de qualidade, otimização dos processos de obtenção, desenvolvimento de novas ligas a fim de conseguir um melhor rendimento, tratamento de água e efluentes e processos regulatórios, entre outras atividades.
Outro abrasivo sintético é o carbeto de cálcio (carbureto), usado tanto na fabricação da cianamida (importante na indústria de polímeros) por combinação com o nitrogênio quanto na obtenção do acetileno pela reação com água.
Alguns materiais extremamente duros ainda exigem o diamante para a abrasão. São os casos de alguns metais, do vidro, da cerâmica e também das pedras preciosas e semipreciosas.
As ferramentas abrasivas têm enorme importância na fabricação de instrumentos metálicos de precisão, automóveis, aviões, armas, canhões e outros produtos industriais.
Os químicos da área de metalurgia buscam desenvolver ligas de dureza cada vez maior e que produzam alta eficiência de abrasão e boa relação de custo-benefício.
Um produto comercializado na forma de aerossol consiste basicamente em uma embalagem dotada de uma válvula, sendo preenchida com o gás que atua como propelente e o concentrado contendo os componentes específicos de cada formulação.
A fabricação dos aerossóis industriais deve ser conduzida e controlada por profissionais da Química. Além de conterem produtos químicos, estes são mantidos sob pressão. O Químico que atua nessa área deve ter conhecimentos sobre o aerossol com relação à sua eficiência, segurança e seus possíveis impactos ambientais nas condições de produção, envasamento, transporte, armazenagem e aplicação do produto.
O estudo do aerossol atmosférico também exige conhecimentos dos profissionais da área de Química. Os impactos ambientais e efeitos prejudiciais à saúde causados pela presença de determinados aerossóis na atmosfera estão relacionados a uma área importante da Química Ambiental. O material particulado atmosférico pode causar diversos impactos negativos como: diminuição da visibilidade, problemas de saúde (especialmente respiratórios), deposição de sujeira em superfícies, além de potencializar a corrosão atmosférica e favorecer a formação de novas espécies de poluentes, a partir de outros poluentes presentes na atmosfera. Como exemplo de poluição causada por aerossóis pode ser citado o Smog Fotoquímico, que é formado a partir da associação entre a neblina e a fumaça. Smog é a junção de duas palavras inglesas: smoke = fumaça e fog = neblina.
Os profissionais da Química também podem atuar na área de Saúde, por meio do estudo da poluição em ambientes internos causada pela emissão de aerossóis. Mais especificamente, essa atuação se dá na área de Segurança do Trabalho e Saúde Ocupacional, por exemplo, em ambientes onde há possibilidade de exposição do trabalhador a atmosferas contaminadas. Nos ambientes industriais, os aerossóis podem ser originados por processos químicos, como combustões, ou físicos, a exemplo de polimentos, pinturas etc. Em outros ambientes, como hospitais e áreas de grande concentração de indivíduos – como nos transportes públicos -, os aerossóis também podem atuar como veículos de propagação de agentes biológicos, como vírus e bactérias.
A indústria de alimentos teve um grande avanço após a Segunda Guerra Mundial (1939-1945), com o advento dos produtos industrializados instantâneos. Essa expansão só foi possível devido ao aprimoramento e desenvolvimento de técnicas de desidratação, congelamento e higienização, entre outras tantas, necessárias ao correto processo de industrialização dos alimentos. Nesse sentido, a criação de novas embalagens também teve papel fundamental para garantir os prazos de validade cada vez mais longos. Isso sem falar das técnicas de embalagem a vácuo que permitem conservar muitos alimentos industrializados sem refrigeração.
Atualmente, há em todo o mundo um crescente interesse pelo papel desempenhado na saúde por alimentos contendo componentes que influenciam em atividades fisiológicas ou metabólicas. Também tem aumentado a procura pelos chamados alimentos funcionais, que são produtos enriquecidos com substâncias isoladas que melhoram o desempenho daquelas atividades.
Os compostos químicos que conferem qualidades a esses alimentos são os fitoquímicos, como os encontrados em plantas (carotenóides, licopenos, xantenos, isotiocianatos, entre outros). Alimentos como tomate, aveia, soja e brócolis, para citar apenas alguns, contêm centenas de compostos biologicamente ativos, sendo que alguns deles têm demonstrado possuir propriedades funcionais. Também enquadram-se nesse grupo os chamados probióticos, alimentos que contém microrganismos vivos capazes de controlar a flora bacteriana intestinal.
Existem cinco mercados principais para os alimentos funcionais industrializados: bebidas e produtos lácteos, produtos de confeitaria, produtos de panificação e cereais matinais. A partir da década de 1990, tais alimentos ganharam um grande destaque, pois essa evolução é atribuída à imagem positiva que possuem em relação ao impacto na saúde e bem-estar, o que os tornou tão populares.
As bebidas alcoólicas são geralmente classificadas em dois grandes grupos: fermentadas e destiladas. As primeiras são produzidas com o auxilio de micro-organismos que se alimentam dos açúcares da matéria-prima (por exemplo, a uva), liberando álcool e gás carbônico. As destiladas, por sua vez, são obtidas depois de passar pela evaporação e posterior condensação do líquido que vai dar origem à bebida, processo no qual são eliminadas as impurezas.
A legislação brasileira faz ainda uma classificação mista das bebidas alcoólicas: fermentadas, por mistura e fermento-destiladas, sendo estas últimas ainda subdivididas em destiladas e destilo-retificadas.
Alguns exemplos:
- fermentadas: cerveja, vinho, jeropiga, vinho de frutas;
- por mistura: licor, amargo e aperitivo, aguardente composta e bebidas mistas;
- destiladas: aguardente de cana ou caninha, aguardente de melaço ou cachaça, rum, uísque, arak (de arroz), conhaque, graspa ou bagaceira, pisco, aguardente de frutas, tequila e tiquira;
- destilo-retificadas: vodca, genebra, gim, steinhaeger, aquavit.
Cervejas – A cerveja é obtida pela fermentação alcoólica de cereal maltado, geralmente malte de cevada, cujo teor alcoólico é baixo – de 3% a 8%. A matérias-primas essenciais para sua fabricação são: água, malte, complementos de malte, levedura e lúpulo. Outros componentes podem ser utilizados, de acordo com o tipo, a tradição ou a preferência local, mas o que diferencia os vários tipos de cerveja encontrados no comércio é a maneira como são processadas as matérias-primas, a quantidade em que são utilizadas, a duração das etapas de fabricação e o processo tecnológico empregado.
A fermentação da cerveja é complexa devido ao número de produtos que são originados, alguns por reações químicas, outros pela ação de micro-organismos. Entre estes últimos produtos predominam o etanol e o gás carbônico, além de glicerol, ácido acético e álcoois. A cerveja contém de 8% a 15% de sólidos, dos quais a maior parte procede diretamente de componentes residuais do caldo em fermentação e de interações entre estes nas diversas etapas da fabricação.
Vinhos – O vinho é um produto da transformação de matéria vegetal viva – a uva – por microrganismos vivos. Desta forma, sua composição, bem como sua evolução, são diretamente ligadas aos fenômenos bioquímicos. Essa definição permite compreender a extrema complexidade de sua composição química e define ainda o valor alimentar do vinho: provindo de células vivas, contém em pequenas quantidades de elementos importantes à vida.
Os vinhos classificam-se em naturais (álcool entre 7% e 14%) ou fortificados (álcool entre 14% e 30%), secos ou doces, suaves ou espumantes. Sua coloração depende, em grande parte, da natureza das uvas e do fato de as cascas serem prensadas ou não antes da fermentação.
Bebidas por mistura – O licor é obtido pela mistura ou redestilação do álcool etílico (que pode ser substituído por cachaça) com substâncias de origem animal (leite, mel) ou vegetal (frutas, ervas) adicionadas a açúcar ou afins.
De maneira geral, a produção de energia a partir da biomassa requer uma área significativamente menor que a exigida para a construção de uma usina hidrelétrica, por exemplo. Além disso, incentiva atividades econômicas locais, como a agroindústria, reduzindo custos, fixando as comunidades em suas áreas de origem e possibilitando o acesso de pessoas isoladas à eletricidade.
Várias comunidades na Amazônia já geram energia a partir da queima controlada dos restos de madeira de pequenas serrarias. Cerca de 50% de cada árvore cortada era perdida em forma de serragem, lascas ou aparas das cascas, antes abandonadas ao apodrecimento.
Por sua vez, a casca de arroz deixou de ser um problema ambiental para a indústria de beneficiamento gaúcha e virou um insumo gerador de energia. Além disso, o subproduto da queima desse material pode ainda ser recuperado como matéria-prima para as indústrias eletrônicas, as de cerâmica e as de vidro.
Já o bagaço da cana-de-açúcar, considerado um estorvo há pouco tempo, hoje é queimado de modo controlado, produzindo calor para a destilação do álcool e vapor para a geração de eletricidade.
Biocombustíveis líquidos:
Álcool Combustível – O etanol brasileiro produzido a partir da cana-de-açúcar é, sem dúvida, o caso de maior sucesso de substituição dos combustíveis fósseis, haja vista o bom desempenho de vendas dos carros bicombustíveis. Com tecnologia 100% nacional, consegue-se obter aproveitamento praticamente total da matéria-prima, convertendo inclusive o bagaço da cana em energia. Isso confere ao nosso álcool um balanço energético altíssimo: cerca de quatro vezes superior ao dos álcoois produzidos nos outros países.
Óleos vegetais in natura – Óleos vegetais in natura, ou seja, sem a mistura de produtos químicos, têm sido utilizados na Europa para mover carros, caminhões e até mesmo locomotivas. Esses óleos vêm de canola, amendoim, soja, girassol e outros produtos bastante conhecidos, o que tem despertado o interesse por tal tecnologia aqui no Brasil.
Com determinados cuidados, como a escolha das plantas oleaginosas a serem exploradas, o tamanho e a localização das plantações, além do controle dos gases resultantes da combustão nos motores, os biocombustíveis representam uma série de oportunidades para o País. Como exemplo, podemos citar os novos investimentos em infra-estrutura produtiva capazes de gerar empregos e renda. Além disso, os óleos são produzidos a partir de insumos abundantes no território brasileiro, o que faz deles produtos 100% verde-amarelos.
Biodiesel – O biodiesel é fabricado pela transesterificação (um tipo de reação química) de óleos vegetais com álcool, geralmente o metanol. No Brasil, há vários grupos de pesquisa estudando maneiras de obter o biodiesel a partir do etanol e dos óleos de variadas oleaginosas _ por exemplo, a mamona, o dendê, e plantas da Amazônia, como o buriti. O biodiesel possui muitas vantagens em relação aos derivados do petróleo. Em algumas regiões, já se começa a adicionar pequenas quantidades desses óleos vegetais ao diesel comum, reduzindo-se a nossa dependência do combustível fóssil.
Biogás – Toda matéria orgânica, como restos agrícolas, esterco e lixo, sofre decomposição por bactérias microscópicas. Durante o processo, elas retiram dessa biomassa aquilo de que necessitam para sua sobrevivência, lançando gases e calor na atmosfera.
O biogás é resultante da decomposição controlada do lixo doméstico, em aterros sanitários, ou do esterco de gado, em recipientes especiais conhecidos como biodigestores. O esgoto das nossas cidades recolhido às estações de tratamento também é uma fonte de biogás, que pode ser utilizado para movimentar ônibus e caminhões ou para produzir eletricidade e calor em cogeradores.
Uma política de geração e aproveitamento do biogás possibilitaria a regularização de milhares de lixões que existem no País, pois para operá-los de maneira controlada seria necessário investir em infraestrutura, drenagem, segurança e mão de obra especializada. Do mesmo modo, o esgoto, que atualmente é jogado em córregos e valas, teria de ser canalizado para estações de tratamento, resultando em ganhos ambientais, sociais e de saúde pública. A boa notícia é que já contamos com aterros sanitários funcionando regularmente e gerando biogás de lixo em cidades como Salvador, São Paulo, Rio de Janeiro e Goiânia.
Outra iniciativa muito importante seria estimular a adoção de biodigestores em áreas rurais, gerando, por exemplo, gás para cocção (cozimento), aquecimento de água ou climatização das maternidades das criações de suínos, a partir dos dejetos destes animais, como já acontece em milhões de propriedades rurais na China e Índia.
As borrachas sintéticas são materiais elastoméricos que possuem capacidade de retornar à forma original quando submetidos a um esforço ou deformação externa, ou seja, são produtos com grande elasticidade. Foram desenvolvidas nas primeiras décadas do século XX nos Estados Unidos e na Alemanha, como substitutas da borracha natural. As borrachas sintéticas têm como base os copolímeros (polímeros derivados de mais de uma espécie de monômero) de estireno e butadieno.
Em seu processamento industrial, as borrachas recebem aditivos, alguns inertes, outros de reforço de estrutura, e alguns que conferem cor, odor e resistência, entre diferentes características. O processamento industrial inclui a vulcanização, que consiste no aquecimento do composto com um agente de vulcanização, geralmente enxofre, e um acelerador de reação (catalisador). Com a vulcanização, o material passa do estado plástico para o elástico e com características definidas e estáveis de dureza, resistência mecânica, elasticidade, entre outras.
A indústria automobilística é a maior consumidora de borrachas, mas outros setores produtivos também se destacam, como os de calçados, mineração e siderurgia, eletroeletrônicos e eletrodomésticos, de entretenimento (para fabricação de brinquedos, máscaras, balões), saúde (para produção de luvas cirúrgicas, preservativos, tubos cirúrgicos, bicos de mamadeira), indústria petroquímica, construção civil e saneamento.
A presença do profissional da química é fundamental na indústria de borrachas. Ele atua no desenvolvimento da formulação da borracha e no controle de qualidade das matérias-primas e dos produtos. Ao receber a matéria-prima ele precisa verificar a qualidade e suas especificações para definir, a partir daí, a melhor formulação para o produto que deseja fabricar. No caso da borracha natural, o profissional da química verifica, por exemplo, o teor de umidade e a presença de contaminantes, que podem interferir no processo produtivo.
A atuação do profissional da química também é fundamental na condução do processo de produção dos artefatos de borracha, já que controla as reações químicas e evita a ocorrência de reações indesejáveis, como a degradação oxidativa ou a decomposição térmica com a formação de outros compostos químicos, o que poderia alterar sensivelmente as características do produto final.
O desenvolvimento e o uso de catalisadores são parte importante da constante busca por novas formas de aumentar o rendimento e a seletividade de produtos, obtidos em de reações químicas. As primeiras menções dessas substâncias datam de 2 mil anos atrás, quando os fabricantes de vinhos, pães e queijos descobriram que era necessário adicionar uma pequena quantidade da partida anterior para fazer um novo lote de um desses produtos.
Todavia, foi somente em 1835 que Berzelius, químico sueco, definiu o fenômeno da catálise que já havia sido observado, indicando que pequenas quantidades de uma origem externa poderiam afetar significativamente o curso de reações químicas. Esta força misteriosa atribuída à substância foi chamada catalítica. Em 1894, expandiu-se a explicação anterior com a afirmação de que catalisadores eram substâncias que agiam sobre a velocidade de reações químicas, sem serem consumidas. Desde os trabalhos de 1835, essas substâncias elas têm desempenhado um importante papel econômico no mercado mundial.
Alguns exemplos de catalisadores:
- A alumina (Al2O3) é utilizada na desidratação de álcoois.
- Elementos como prata (Ag), cobre (Cu), platina (Pt), ferro (Fe), níquel (Ni) e seus óxidos, bem como o dióxido de manganês (MnO2), são utilizados em reações de oxidação.
- O fosfato de níquel, o cálcio e o óxido de crômio catalisam a desidrogenação de um derivado de petróleo chamado butano. Esse processo é usado na formação do butadieno industrial que, por sua vez, é empregado na produção de borracha sintética.
Dependendo do seu destino, ela ainda passa por operações de lavagem, peneiramento e branqueamento. Se a própria indústria que extraiu a celulose fabrica o papel, ela pode dispensar a secagem e usar um sistema de tubulação para conduzir a massa celulósica diretamente para a refinação. Nos casos em que a celulose é vendida para outras empresas produzirem o papel, no entanto, serão imprescindíveis a secagem e o enfardamento.
As propriedades do papel são resultantes de interações de um grande número de fatores, tais como: fibras ou misturas de fibras usadas; processo de obtenção da pasta celulósica; matérias-primas não fibrosas; tratamento térmico; preparação da massa e processo de formação da folha. Estas variáveis devem ser ajustadas por um profissional qualificado para que se obtenha um produto com as propriedades desejadas.
Certas características do papel, como, por exemplo, a resistência à umidade, só podem ser obtidas com a adição de aditivos químicos. Estas propriedades são afetadas tanto com a incorporação dos aditivos na massa quanto na aplicação do produto no revestimento.
Os processos cerâmicos podem ser classificados em “cerâmica tradicional” e “cerâmica avançada” (cerâmica fina ou cerâmica de alta tecnologia). Na cerâmica tradicional, as matérias-primas geralmente são utilizadas após beneficiamento, ou seja, separação de impurezas por processos físicos. De modo geral, não são submetidas a reações químicas, portanto, considera-se que a matéria-prima é natural. Já no caso das cerâmicas avançadas, normalmente, trabalha-se com matérias-primas sintéticas, ou seja, obtidas por meio de reações químicas.
A cerâmica tradicional engloba a maior parte da produção cerâmica, pois utiliza matérias-primas de baixo custo e abundantes na natureza, como argilas, feldspatos, calcários e outros minerais cristalinos inorgânicos não metálicos. Envolve os processos de fabricação de cerâmica estrutural, tais como: tijolos, telhas e blocos; revestimentos, como pisos e azulejos; cerâmica branca, como louça sanitária, de mesa ou artística, entre outros.
As cerâmicas avançadas, por sua vez, são utilizadas nas mais diversas áreas, tais como:
- bioquímica: em implantes dentários e substituição de ossos;
- eletroeletrônica: em sensores, sonares, supercondutores e capacitores;
- mecânica: em ferramentas de corte, membranas;
- ótica: em fibras óticas, material fluorescente;
- térmica: como substratos;
- nucleares: nos combustíveis.
Os abrasivos, o cimento e a cal também podem ser considerados segmentos do setor cerâmico, assim com os corantes, os vidros e as fritas. Estas últimas nada mais são do que vidro moído obtido à partir da fusão de uma mistura de várias matérias primas e aplicado na superfície do material cerâmico. Após a queima, adquirem aspecto vítreo e conferem à peça melhor aparência, impermeabilidade e aumento da resistência mecânica.
O grupo dos materiais cerâmicos inclui ainda os refratários, materiais que apresentam resistência mecânica, a temperaturas elevadas, a variações bruscas de temperatura, etc. Em termos de processamento de matérias-primas e custo final, ocupam uma posição intermediária entre as cerâmicas tradicionais e as avançadas. São obtidos de matérias-primas como sílica, aluminas, mulita, carbeto de silício, grafita, carbono, espinélio e outros. São utilizados na fabricação de fornos, churrasqueiras, lareiras e também como isolantes térmicos.
Para que uma substância possa ser usada como cola, deve satisfazer aos seguintes requisitos gerais:
- Aderir bem às superfícies a serem unidas, quase como se executasse uma “fusão química” sobre os materiais;
- Completar os seus processos de endurecimento num tempo razoável, sem exigir a aplicação de temperaturas e pressões excessivas;
- Manter os materiais unidos, mesmo sob esforços mecânicos.
Antes do surgimento da indústria química e das colas sintéticas, o homem já utilizava colas naturais: cera de abelha, resina, borracha e goma-laca (produzida por insetos parasitas que vivem em árvores). Acredita-se que os marceneiros egípicios tenham sido os primeiros a produzir uma cola, a partir de restos de animais, como espinhas de peixe, cascos, chifres, ossos, peles e tendões. As colas vegetais feitas de goma liberada por certas árvores e plantas, as colas à base de látex da borracha e as colas obtidas a partir do amido também possuem origem antiga.
Alguns desses produtos naturais continuam sendo usados, principalmente nas marcenarias, mas as colas sintéticas à base de resinas acrílidas, vinílica,epoxi etc dominam o mercado atual. Têm aplicações em diversos seguimentos industriais, desde celulose e papel até automóveis e aviões.
O trabalho dos químicos na indústria cosmética não se limita a aplicar fórmulas, mas consiste também em pesquisar e desenolver novos produtos, essenciais para garantir o espaço da empresa no mercado. Uma das maiores fábricas de cosméticos do Brasil registrou que 63% de seu faturamento de 2004 veio de produtos lançados nos dois anos anteriores. Por isso, esta e muitas outras empresas investem constantemente na inovação e ampliação de sua linha de produtos.
Outra função vital do químico nas indústrias do setor é o controle de qualidade da água, sua matéria-prima principal, tanto do ponto de vista químico quanto microbiológico. Para a produção de cosméticos, é necessária a avaliação diária do pH, condutividade e teor da substância antimicrobiana utilizada na sua descontaminação. Se houver um descuido no controle de qualidade, a água pode chegar à linha de produção com altas concentrações de cálcio, magnésio, ferro e zinco, entre outros. Em loções pós-barba, por exemplo, tais substâncias podem provocar a formação de resíduos que comprometem a qualidade do produto.
Alguns dos produtos formulados são obtidos por simples mistura dos componentes; outros, passam por reações químicas. Para conduzir esses processos, as indústrias de defensivos agrícolas precisam contar com profissionais da química. A presença deles também é imprescindível no controle de qualidade dos produtos – que envolve análises químicas e físico-químicas – e no tratamento de resíduos para evitar a contaminação do meio ambiente.
Até mesmo na agricultura orgânica são empregados defensivos agrícolas. A aplicação de caldas bordalesa e sulfocálcica são os principais métodos empregados pelo agricultores adeptos desse sistema de produção para combater pragas e doenças. Embora essas caldas possam ser produzidas pelo próprio agricultor, foi preciso conhecimento químico para chegar às suas fórmulações.
A calda bordalesa, por exemplo, surgiu no final do século XIX, quando um agricultor francês percebeu que a aplicação de água com cal nas parreiras evitava que as uvas fossem acometidas por uma doença chamada antracnose. Estudando a composição química da mistura criada pelo vinicultor, pesquisadores descobriram que seu efeito estava associado ao fato de ela ser produzida em tachos de cobre. A partir daí, chegou-se à formula da calda bordalesa: água + cal + sulfato de cobre.
O principal trabalho dos químicos nas indústrias de essências é a obtenção do óleo essencial e sua transformação em essência. Isso é feito basicamente por processos de separação de misturas, o que pode ser uma tarefa bastante minuciosa, se considerarmos que alguns óleos chegam a conter mais de 30 substâncias diferentes. Além disso, desenvolvem formulações que originam novos aromas.
Para obtenção dos óleos, os profissionais da química usam técnicas de separação diferentes, de acordo com o material do qual se pretende extrair a essência. O mais antigo é a destilação, que pode ser simples ou por arraste de vapor, uma técnica que permite melhores resultados.
A prensagem, também conhecida como extração por espremedura, é ideal para extrair o óleo essencial armazenado em cascas de frutas cítricas. Já o processo de enfloragem, que se baseia na propriedade das gorduras e dos óleos de absorver e reter princípios aromáticos sem alterá-los, é usado para obter essências a partir das flores.
Outra técnica é a maceração, que consiste em submeter um corpo sólido qualquer à ação de um líquido (água ou álcool etílico) com o qual se deixa em contato durante um tempo mais ou menos prolongado a fim de que ele dissolva alguns princípios aromáticos do corpo sólido. Esse processo é utilizado para obter várias matérias-primas importantes para a indústria de perfumes, como os bálsamos, as gomas e os óleos-resinas, produtos que geralmente possuem odor agradável, suave e persistente.
Atualmente, utilizando técnicas sofisticadas de separação de misturas, é possível identificar todos os componentes de um óleo essencial, mesmo aqueles que estão presentes em quantidades muito pequenas. Uma vez identificados os componentes, é possível fabricar o óleo essencial sintético que é geralmente mais barato e, muitas vezes, mais fácil de se obter.
No entanto, sua fabricação requer rígido controle das condições do processo de manutenção preventiva dos equipamentos, pois um evento explosivo não esperado ou não controlado é quase uma catástrofe para os equipamentos e para o pessoal afetado. Portanto, uma indústria de explosivos deve selecionar profissionais extremamente conscientes dos riscos e zelosos pela rígida observância das normas. Rotinas de trabalho devem ser seguidas à risca, pois elas foram forjadas levando em consideração a correção dos erros ocorridos que levaram ou não a acidentes.
Aplicabilidade:
Mineração – desmonte de rochas.
Engenharia – implosões de edifícios, abertura de valas, canais e estradas.
Siderurgia – ruptura do selo do cadinho para o escoamento do aço fundido.
Indústria espacial – propelente sólido de foguetes e nos geradores de gases de satélites.
Automotiva – nos air-bags e nos cintos de segurança.
Indústria de defesa – foguetes, mísseis, munições e acessórios.
Indústria de sinalizadores – dispositivos de cores e som para marcação de pontos enfim materiais de salvatagem.
Indústria de fogos de artifício – fogos de estampido, cores, cascatas, chuvas de cores. É um espetáculo! Vide a passagem de 31 dezembro a 1º janeiro.
Indústria farmacêutica – a nitroglicerina é utilizada (ppm) como um eficiente vasodilatador.
Segurança contra incêndios – em pequenas cápsulas que, ao sentirem a presença de fogo, explodem liberando a passagem de água nos espargidores “sprinklers”.
Assim, a produção de medicamentos em escala industrial por meio da preparação de misturas medicamentosas é apenas a fase final de um processo. Sua produção caracteriza-se como um processo biotecnológico ou químico de síntese orgânica. A síntese a partir de compostos químicos, como os carboquímicos, petroquímicos, e outros, é a principal atividade das indústrias farmoquímicas. Elas integram o setor de “química fina”, um dos que exigem pessoal mais qualificado e equipamentos com tecnologia de ponta.
Os Profissionais da Química contribuem muito para o desenvolvimento de novos medicamentos, desde a descoberta até a síntese de princípios ativos. Alguns deles, inclusive, foram ganhadores de prêmios Nobel, como Satoshi Ōmura, William C. Campbell e Youyou Tu, laureados em 2015 em Medicina e Fisiologia pelas descobertas de novos tratamentos contra parasitas. Clique aqui para ler artigo publicado sobre este assunto no Informativo CRQ-IV.
Na indústria farmacêutica, o Profissional da Química exerce várias funções com a finalidade de possibilitar a combinação do princípio ativo com outras substancias que o tornem próprio para consumo e melhorem sua biodisponibilidade. Afinal, para o desenvolvimento de medicamentos são necessários conhecimentos de estrutura molecular, propriedades físico-químicas e síntese orgânica dos fármacos. Além disso, o controle de qualidade é realizado basicamente por meio de análises químicas, físico-químicas e microbiológicas, entre as quais podemos citar: teor de princípio ativo, teor de pureza, índice de acidez, teor de álcool, pH, contagem de micro-organismos patogênicos.
O Profissional da Química, devido à sua formação técnico-científica, possui habilitação para ocupar cargos de responsabilidade na indústria farmacêutica, em setores como produção, controle de qualidade físico-químico e microbiológico, e garantia da qualidade.
O trabalho dos químicos é fundamental na produção de fertilizantes. O nitrogênio, por exemplo, é encontrado em abundância na natureza, mas, na forma como se apresenta, as plantas não conseguem absorvê-lo. Por isso, foram desenvolvidos compostos químicos que passaram a ser a principal forma de fixar o Nitrogênio e torná-lo disponível para os vegetais.
O mesmo ocorre com os fertilizantes fosfatados. Na maioria dos casos, sua matéria-prima – a rocha fosfática – precisa ser tratada para aumentar o teor de minério. O superfosfato, um fertilizante bastante usado, por exemplo, é obtido a partir de reações químicas que, além do concentrado de fósforo, usam os ácidos sulfúrico ou fosfórico.
A matéria-prima dos fertilizantes potássicos, a silvinita, também passa por processos químicos para obtenção do minério de potássio. Os mais usados são os métodos de separação de misturas como a flotação, a separação por meios densos e a dissolução-cristalização.
Até mesmo os fertilizantes orgânicos passam por processos químicos, embora também possam ser utilizados in natura. A compostagem – uma fermentação controlada –, é frequentemente usada em resíduos vegetais (folhas, ramos) para obter produtos mais estáveis. Outra possibilidade é, depois da compostagem, enriquecer o fertilizante orgânico com nutrientes como os que já citamos.
Vários materiais podem ser usados como fertilizantes orgânicos: estercos de aves, suínos e bovinos; resíduos da indústria alimentícia e de óleos, além dos resíduos vegetais. Até mesmo o lixo e o lodo dos esgotos domésticos já podem ser transformados em adubo.
Utilizando processos de compostagem e maturação, a Embrapa (Empresa Brasileira de Pesquisa Agropecuária) conseguiu transformar o lodo, combinado com resíduos vegetais, num adubo orgânico que não agride o meio ambiente. Para chegar nesse material, houve um acompanhamento de processo através de análises químicas convencionais e técnicas laboratoriais avançadas, que utilizam campos magnéticos e radiofrequência, entre outras. Com a produção desse fertilizante, encontrou-se uma alternativa para o problema da geração de lodo doméstico.
A criogenia tem aplicações na propulsão de foguetes, no processamento eletrônico de dados, na fotóptica a infravermelho, no campo dos materiais magnéticos e no bombeamento a alto vácuo. Na indústria química, emprega-se a criogenia para a obtenção de nitrogênio e oxigênio; na metalurgia, para a produção do aço.
Outros gases industriais importantes: amônia, hélio, acetileno, dióxido de enxofre, óxido nitroso e monóxido de carbono.
Confira, abaixo, os componentes, as características e os usos das principais ligas metálicas:
Liga | Componentes | Características | Usos |
---|---|---|---|
Latão | Cobre e zinco | Resistência à corrosão | Navios e tubos |
Bronze | Cobre e estanho | Resistência à corrosão | Moedas e sinos |
Aço | Ferro e carbono | Resistência à corrosão | Navios e utensílios domésticos |
Aço inoxidável | Aço e cromo | Resistência à corrosão | Talheres e utensílios domésticos |
Aço níquel | Aço e níquel | Resistência mecânica | Canhões e material de blindagem |
Aço tungstênio | Aço e tungstênio | Alta dureza | Brocas e pontas de caneta |
Alnico | Aço, alumíni, níquel e cobalto | Propriedades magnéticas | Fabricação de imãs |
Amálgama | Mercúrio, prata e estanho | Resistência a desgaste | Restauração de dentes |
Ouro 18 quilates | Ouro e cobre | Alta ductilidade e maleabilidade | Joias |
Prata da lei | Prata e cobre | Aumento da dureza | Utensílios domésticos e ornamentos |
Eléctron liga de magnésio | Magnésio, alumínio, manganês e zinco | Resistência mecânica e térmica | Peças muitos leves |
Os metais apresentam algumas propriedades que variam conforme sua natureza e fazem com que eles sejam úteis para variadas aplicações . Os de maior brilho, são usados em joalherias e na fabricação de moedas; os que apresentam dureza e densidade são empregados também em instrumentos e aparelhos de implantes cirúrgicos; outra propriedade a ser considerada é a condutibilidade elétrica cujos diferentes graus são muito importantes para várias funções.
Embora o plástico e as cerâmicas venham sendo largamente utilizados, não são capazes de substituir os metais em certas atividades. É por essa razão que eles ainda ocupam lugar de destaque no cenário mundial.
Existem muitas ferramentas disponíveis para o gerenciamento de resíduos, sendo que a ordem de prioridades de medidas a serem adotadas para que se obtenham resultados é a seguinte:
- Prevenção da poluição;
- Reutilização;
- Reciclagem;
- Recuperação de energia;
- Controle de poluição;
- Disposição: descarte em aterros, incineração, etc;
- Remediação: reparação de danos causados ao meio ambiente.
A poluição do ar atmosférico e também do solo, causada pelos produtos químicos usados na agricultura, pelos resíduos industriais e domésticos faz com que a degradação do meio ambiente seja visível e que os efeitos sejam sentidos por todos os seres vivos.
Podemos dividir o meio ambiente em três áreas: água, ar e solo. Em todos eles, os profissionais da química são os responsáveis pelo gerenciamento e controle ambiental, executando os tratamentos de água, ar, efluentes líquidos e resíduos sólidos. Também cabe a eles a caracterização físico-química e a destinação dos poluentes, através de análises laboratoriais, o desenvolvimento de projetos destinados a reduzir a emissão de agentes químicos agressivos ao meio ambiente, bem como para a evolução dos métodos de remediação e biorremediação ambiental.
Por não possuírem conhecimentos profundos sobre todas as áreas, os juízes podem recorrer a profissionais com formações específicas para ajudá-los a compreender melhor os fatos que estão sendo discutidos nos processos. Esses profissionais são chamados de peritos e sua função é elaborar laudos técnicos que podem ser determinantes na tomada de decisão pelo juiz. Uma perícia na área química pode envolver a realização de análises laboratoriais, vistoria de processos, exames de documentos, questionamento de pessoas envolvidas, dentre outros.
Na esfera criminal, os peritos são funcionários públicos concursados, atuando no Instituto Medico Legal, Instituto de Criminalística ou na Polícia Federal (ver Química Forense).
Já nas áreas cível e trabalhista esse vínculo empregatício não existe. Pode ser nomeada para a função de perito qualquer pessoa habilitada, isto é, com nível superior e registrado no respectivo ao conselho profissional. No caso dos profissionais da química, esse registro deve ser feito no Conselho Regional de Química onde tramita o processo.
Além de conhecimento químico, é importante que o perito possua noções de direito a fim de adequar seu trabalho às exigências legais e às formalidades jurídicas. Não é necessário, porém, que ele também tenha formação em Direito.
O Poder Judiciário busca os profissionais da química em bancos ou cadastros, como Banco de Peritos do CRQ-IV, ou associações de classe, como a Associação dos Peritos Judiciais do Estado de São Paulo (Apejesp). Os profissionais que desejarem atuar como peritos também podem se credenciar diretamente nas varas mediante apresentação de documentos específicos.
Além do perito nomeado pelo juiz, o processo também pode contar com a participação de outros profissionais contratatos pelas partes para assessorá-las. Nesta condição, esses especialistas são denominados assistentes técnicos.
Quanto à remuneração, o perito informa o quanto deseja receber de honorários pelo seu trabalho. Se as partes concordarem, o valor é fixado pelo juiz. Já a remuneração do assistente técnico é estabelecido diretamente entre o profissional e a parte que o contratou.
Para definir seus honorários, os profissionais que atuam como peritos ou assistentes técnicos podem se basear em tabelas produzidas por entidades como a Apejesp e o Instituto Brasileiro de Avaliações e Perícias de Engenharia de São Paulo (Ibapesp). Tais tabelas, porém, têm caráter sugestivo, não estando o profissional obrigado a segui-las.
O petróleo e o gás natural são fontes, por excelência, das indústrias petroquímicas, as quais produzem matérias-primas que, muitas vezes, passam por segundos e terceiros processos de transformação antes de serem empregadas na fabricação do produto final. Por isso mesmo, o setor é dividido nos seguintes segmentos:
- Indústrias de 1ª geração: as que utilizam as matérias-primas (nafta, gás natural, GLP, gás de xisto etc) para gerar os produtos ou matérias-primas básicas.
- Indústrias de 2ª geração: aquelas que, a partir de matérias-primas básicas, produzem intermediários que serão matérias-primas para outras indústrias, embora também já possam ter uma aplicação final nesta fase.
- Indústrias de 3° geração: aquelas que constituem o setor de manufaturados.
- Indústrias de 4° geração: as chamadas indústrias de ponta, que utilizam os manufaturados como componentes de suas montagens industriais ou para itens bem especializados de suas atividades, bem como para as especialidades químicas (matérias-primas para indústrias como a cosmética, a farmacêutica e a veterinária).
Um bom exemplo de como os derivados do petróleo percorrem todas essas indústrias antes de se transformarem em produtos finais é a fabricação do PVC (cloreto de polivinila). Na cadeia de transformação dele, as duas matérias-primas iniciais, o eteno e o cloro (1ª geração) primeiramente dão origem ao dicloroetano-DCE (2ª geração), que constitui matéria-prima para a produção do monômero de cloreto de vinila-MVC (3ª geração), que, por sua vez é usado na fabricação do PVC (4ª geração).
Pode-se afirmar que a indústria petroquímica propriamente dita está contida na primeira e na segunda gerações; a terceira e a quarta constituem os seus mercados. A tabela abaixo traz, de forma bem resumida, uma relação das matérias-primas da indústria petroquímica e suas transformações em produtos acabados, que podem ser aproveitados diretamente ou passar por outros processos de transformação, dando origem à imensa variedade de substâncias utilizadas na indústria.
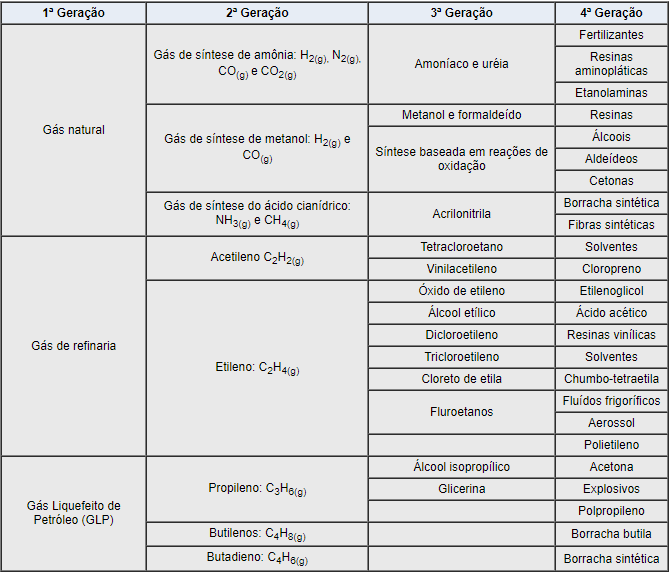
O nome petróleo significa óleo de pedra, porque o petróleo é encontrado, normalmente, impregnado em determinadas rochas porosas denominadas arenito, em camadas geológicas sedimentares, situadas na maior parte das vezes abaixo do fundo do mar.
A teoria mais aceita sobre a origem do petróleo afirma que se trata de um produto da decomposição lenta de pequenos seres marinhos – em geral animais e vegetais unicelulares -, soterrados há pelo menos 10 milhões de anos, que sofreram nesse período a ação de bactérias, do calor e da pressão.
A bateria usada em automóveis, por exemplo, é constituída por placas de chumbo, na forma de grade perfurada. O peróxido de chumbo constitui a placa positiva e o chumbo esponjoso a placa negativa, quando a bateria está carregada. As chapas são isoladas por separadores que podem ser de vidro. A bateria fica cheia como ácido sulfúrico.
Em alguns casos, mais do que para baratear produtos, os polímeros serviram para melhorá-los. Geladeiras antigas, por exemplo, mantinham suas temperaturas baixas com espessas camadas de lã de vidro que eram colocadas no interior das grossas paredes do aparelho. Com a substituição da lã de vidro por um polímero chamado poliuretano, foi possível melhorar o isolamento térmico, o que fez cair o consumo de energia elétrica e, ao mesmo tempo, diminuir a espessura das paredes, liberando mais espaço dentro da geladeira para o armazenamento de alimentos. Neste exemplo, vale lembrar também que este eletrodoméstico, assim como muitos outros, deixou de ser artigo de luxo e hoje estão em praticamente todos os lares.
Polímeros também são encontrados em móveis, tecidos, paredes e em uma imensa gama de produtos sintéticos. Também são adicionados a outros materiais para conferir-lhes características especiais. Os cabos de madeira dos talheres só podem ser lavados sem estragar porque uma resina polimérica os impermeabiliza.
Profissionais preparados para trabalhar com materiais poliméricos, os profissionais da Química são necessários nas indústrias que produzem polímeros e em parte das que utilizam esse material na fabricação de seus produtos, as chamadas indústrias de transformação. Com os polímeros sendo utilizados em um número cada vez maior de bens de consumo, cresce a sua indústria e, consequentemente, as oportunidades de trabalho para esses profissionais.
Atualmente, um dos grandes desafios para a comunidade científica química é criar soluções para o descarte dos polímeros, uma vez que, devido à sua decomposição lenta, estes acabam provocando sérios problemas ambientais. Por isso, estão sendo desenvolvidas pesquisas no campo da reciclagem e criando-se produtos biodegradáveis. Esses trabalhos estão sendo feitos por profissionais da Química e devem contribuir para que produtos e subprodutos industriais de todos os tipos voltem ao ciclo de produção, com consequente renovação das fontes de matéria-prima.
Nanotecnologia, biotecnologia e outras especialidades científicas também vêm contribuindo para o avanço da área de polímeros no desenvolvimento de novos materiais e novos processos, exigindo constante aprimoramento e atualização dos profissionais da área.
O profissional que atua na área de polímeros pode desenvolver novos materiais ou novas técnicas para transformá-los nos mais diversos tipos de artefatos. Dentre as diversas habilidades e competências, ao longo de suas atividades estes profissionais planejam, operam, controlam, coordenam e monitoram o processo de fabricação de produtos de plástico e de reciclagem; supervisionam a aquisição de matéria-prima e controlam a qualidade do produto acabado; realizam ensaios físicos, identificam a composição do material de produtos acabados e elaboram o dimensionamento das necessidades da instalação industrial.
Serviços Laboratoriais
- Realizar pesquisas;
- Desenvolver produtos;
- Realizar análises químicas, físico-químicas, químico-biológicas, bromatológicas (de alimentos), toxicológicas e sanitárias.
Serviços de Consultoria Técnica
- Desenvolver produtos e processos;
- Realizar assistência técnica a clientes;
- Tratar de assuntos regulatórios ou de documentação técnica.
Serviços de Consultoria Ambiental
- Caracterizar resíduos;
- Realizar tratamento de água;
- Realizar o tratamento e destinação de resíduos;
- Reciclar resíduos;
- Analisar solo para determinação da composição química e contaminantes;
- Analisar risco ambiental;
- Gerenciar programas de monitoramento e controle ambiental;
- Avaliar o ambiente da empresa no que diz respeito à segurança do trabalhador.
Serviços de Dedetização
- Especificar produtos químicos utilizados nos serviços de limpeza, higienização e controle de pragas;
- Controlar o manuseio e a aplicação destes produtos.
Armazenagem e Transporte de Produtos Químicos
- Acondicionar adequadamente os produtos químicos;
- Indicar procedimentos de segurança;
- Orientar como agir em caso de acidentes, a fim de evitar danos ao meio ambiente e à saúde pública.
Serviços Ligados ao Ensino
- Lecionar disciplinas técnicas das diversas áreas da Química;
- Orientar trabalhos de conclusão de cursos.
Serviços de Pesquisa
- Desenvolver novos produtos;
- Melhorar produtos existentes.
Venda Técnica
- Verificar as necessidades do cliente em relação a um produto/equipamento;
- Apresentar tecnicamente um produto/equipamento ao cliente.
Existem ainda os produtos da chamada química fina, que exigem o trabalho de profissionais altamente capacitados. É o caso dos fármacos que contém os princípios ativos de medicamentos e dos aromatizantes da indústria alimentícia.
As empresas e os profissionais que trabalham com este segmento da química têm alta responsabilidade justamente porque produzem insumos para alimentos e medicamentos. Os equipamentos que utilizam são de alta precisão, uma vez que é necessário ter controle total de todas as etapas do processo produtivo.
*Conversão feita com base na cotação do dólar em 02/02/2006.
A Química Forense engloba análises orgânicas e inorgânicas, toxicologia, investigações sobre incêndios criminosos e sorologia. Suas conclusões servem para embasar decisões judiciais.
Apesar de as investigações criminais serem o aspecto mais conhecido da Química Forense, ela não se limita a ocorrências policiais. O químico forense também pode dar seu parecer em decisões de natureza judicial, atuar em questões trabalhistas, como determinar se uma atividade é perigosa ou insalubre, detectar adulterações em combustíveis e bebidas, uso de drogas ilícitas, fazer perícias em alimentos e medicamentos e investigar o doping esportivo.
O que fazem os químicos forenses?
O químico forense trabalha analisando amostras colhidas das vítimas ou dos locais de crimes e ocorrências. Uma de suas tarefas principais é fazer análises especializadas para identificar materiais e conhecer a natureza de cada prova relacionada a um possível crime.
Por lidar com grande variedade de provas e amostras, o químico forense deve ter conhecimentos sólidos de todas as áreas da Química, principalmente de Química Orgânica e Bioquímica, já que terá de analisar, com frequência, fluidos de origem biológica. Ele também precisa ter conhecimentos suficientes para decidir que tipo de análise será feita dependendo das amostras disponíveis e quando é necessário buscar provas ou amostras adicionais. Para isso, precisa manter-se permanentemente atualizado.
O químico forense trabalha como perito para as polícias civis de todos os estados brasileiros e para a Polícia Federal. Sua formação nestes casos se dá em cursos específicos oferecidos pelas academias de polícia, que incluem conteúdos de Química Forense e Biologia Forense.
Outras matérias-primas dos refrigerantes são os conservantes, que impedem ou retardam a deterioração provocada por microrganismos, como leveduras, mofos e bactérias; os acidulantes, que regulam a doçura do açúcar, intensificam o gosto ácido, controlam o pH e inibem a proliferação de microrganismos; os antioxidantes, que impedem a ação do oxigênio causador da perda da cor e deterioração do produto. Também são utilizados aromatizantes, que conferem ou intensificam o aroma; flavorizantes, que conferem ou intensificam tanto o sabor quanto o aroma; e corantes, para dar ou intensificar a cor dos refrigerantes. O gás carbônico realça o paladar e dá a impressão sensorial de gasoso/efervescente e melhora a aparência do produto.
Os refrigerantes são vendidos em embalagens de PET poli(tereftalato de etileno), garrafas de vidro e latas, em volumes que variam de 237 mililitros a 3 litros, e também em barris de aço ou alumínio. Existem refrigerantes de muitos sabores, como guaraná, laranja, limão, cola, abacaxi, uva, maçã, framboesa e tutti-frutti. O sabor preferido em todo o mundo é o cola. No Brasil, os sabores preferidos são, pela ordem, cola, guaraná, laranja, limão e uva.
Fabricação – As etapas de fabricação dos refrigerantes incluem o tratamento da água, a elaboração do xarope simples, que consiste na dissolução do açúcar em água quente; a preparação do xarope composto, quando o xarope simples é misturado aos outros ingredientes; e a elaboração de análises microbiológicas e físico-químicas. Na fase final da fabricação o xarope composto segue até a linha de envasamento e passa por uma sequência de máquinas: cuba de mistura, onde o xarope é misturado com a água; gaseificador, onde recebe o CO2; enchedora, arrolhador, rotuladora e empacotadora, até chegar ao estoque para distribuição. Esteiras movimentam as embalagens vazias e cheias entre os diversos pontos da operação.
Durante o processo de fabricação os refrigerantes passam por vários processos de controle. Os testes da água têm o objetivo de realizar o controle microbiológico e a retirada do cloro antes do uso. O xarope simples e o composto passam por análises de acidez, cor, turbidez, concentração e detecção da presença de microrganismos.
Na fase final, depois de todos estes controles físico-químicos, ainda é feito o controle de linha de produção, que inclui a checagem de itens como carbonatação, cor, brix (concentração) no mínimo a cada 20 minutos para garantir padrões de qualidade preestabelecidos. A acidez é testada nos tanques de xarope composto.
Além disso, é feito um acompanhamento visual para detecção de resíduos nas garrafas. Também é feita a retenção de algumas garrafas a cada dia ou a cada lote produzido para acompanhamento dos parâmetros físicos, químicos e microbiológicos.
Os profissionais da Química estão presentes em todas as etapas de produção de refrigerantes, atuando no controle de qualidade desde a entrada das matérias-primas até o descarte dos efluentes. O trabalho do químico é muito extenso e envolve todo o processo, pois é importante manter padrões de qualidade no momento e após a produção.
Nesta área, o Profissional da Química tem inúmeras responsabilidades, desafios e possibilidades de atuação profissional. Desenvolvimento de novos produtos que atendam a uma nova demanda de tempo, técnicas e substratos de utilização; pesquisa e produção de matérias-primas que componham fórmulas cada vez mais de acordo com a sustentabilidade; criação de embalagens que favoreçam o armazenamento e a utilização do produto; atenção às novas tecnologias de novos componentes e processos de fabricação são alguns dos campos em que a Química e seus profissionais se fazem presentes.
Conhecer e aplicar tanto a legislação regulamentadora quanto as atualidades em relação à toxicologia dos componentes presentes em produtos também são atribuições dos profissionais da área química.
A história do sabão
A fabricação de sabão é, sem dúvida, uma das atividades industriais mais antigas de nossa civilização. Sua origem remonta a um período anterior ao século XXV a.C.. Nesses mais de 4.500 anos de existência, a indústria saboeira evoluiu, acumulando enorme experiência prática, além de estudos teóricos desenvolvidos por pesquisadores.
Tecnicamente, a indústria do sabão nasceu muito simples e os primeiros processos exigiam muito mais paciência do que perícia. Tudo o que tinham a fazer, segundo a História, era misturar dois ingredientes: cinza vegetal, rica em carbonato de potássio, e gordura animal. Então, era esperar por um longo tempo até que eles reagissem entre si. O que ainda não se sabia era que se tratava de uma reação química de saponificação.
O sabão, na verdade, nunca foi “descoberto”, mas surgiu gradualmente de misturas de materiais alcalinos e matérias graxas (alto teor de gordura). Os primeiros aperfeiçoamentos no processo de fabricação foram obtidos substituindo as cinzas de madeira pela lixívia, rica em hidróxido de potássio e obtida passando água através de uma mistura de cinzas e cal. Porém, foi somente a partir do século XIII que o sabão passou a ser produzido em quantidades suficientes para adquirir escala industrial.
Até o princípio do século XIX, pensava-se que o sabão fosse uma mistura mecânica de gordura e álcali. Foi quando Chevreul, um químico francês, mostrou que a formação do sabão era na realidade uma reação química. Nessa época, Domier completou estas pesquisas, recuperando a glicerina das misturas da saponificação.
Durante 2 mil anos, os processos básicos de fabricação de sabões permaneceram praticamente imutáveis. As modificações maiores ocorreram no pré-tratamento das gorduras e dos óleos, na obtenção de novas e melhores matérias-primas, no processo de fabricação e no acabamento do sabão, por exemplo, na secagem por atomização para obtenção do sabão em pó.
Os profissionais da química também atuam na fiação e tecelagem, de modo especial no desenvolvimento das fibras sintéticas. Suas atividades, no entanto, concentram-se na fase de acabamento, quando são usadas enzimas, soda cáustica e uma série de outros produtos e processos químicos.
Dependendo das condições em que os fios saem da tecelagem e do destino que lhes será dado, os profissionais da química desenvolvem tratamentos para que eles adquiram as características desejadas. Um deles é a desengomagem que, como sugere o nome, é usada para eliminar engomantes adicionados aos fios durante o tecimento para aumentar sua resistência. Depois de formado o tecido, no entanto, esses engomantes precisam ser eliminados, uma vez que formam uma camada sobre o tecido que impede a penetração de produtos usados nos banhos para acabamento. A desengomagem é feita com enzimas, num processo no qual a temperatura, o pH e a concentração dos produtos utilizados precisam ser rigorosamente controlados. Daí a importância do acompanhamento constante de um profissional da química
Tal como os engomantes, resíduos que aderem ao tecido durante sua fabricação, tais como poeiras, óleos e graxas, também dificultam os processos de acabamento. Por isso, eles são removidos num processo de limpeza conhecido como purga, que envolve produtos químicos como alvejantes, desengraxantes, detergentes e solventes.
Feitos estes e outros pré-tratamentos que forem necessários, parte-se para o tingimento. Esta é uma etapa que requer acompanhamento constante, quer no controle das matérias-primas utilizadas, tais como alvejantes, amaciantes, pigmentos e resinas, quer no controle dos parâmetros do processo de tingimento em si.
Se além de cor, for necessário aplicar uma estampa ao tecido desenvolve-se uma tinta em forma de pasta, combinando solventes, pigmentos e outros produtos. Essa combinação deve ser feita por um químico, que avaliará quais elementos e em que quantidade devem ser empregados para se obter o efeito desejado.
Outra função importante do profissional da química nas indústrias têxteis é o tratamento dos efluentes gerados no processo produtivo. Para evitar que ocorram danos ao meio ambiente, a água que será descartada passa por análises para controlar, principalmente, o pH, a concentração de pigmentos e a temperatura. De acordo com as conclusões das análises, serão usados processos de clarificação, neutralização e resfriamento, entre outros, de modo que a água a ser eliminada não polua o meio ambiente.
As fases da fabricação são as seguintes:
- Pesagem das matérias-primas de acordo com a formulação: consiste na formação de pastas do veículo e do pigmento (dispersão), formando a pré-mistura;
- Moagem: consiste na passagem da pré-mistura em moinhos, em especial moinhos de areia;
- Completagem: consiste na etapa de adição e ajuste dos constituintes, especialmente solvente, até a proporção desejada;
- Acertos finais: consistem no acréscimo de aditivos, acertos de cores e outros necessários para definição do produto final.
Para execução destas operações, uma fábrica de tintas é, em geral, constituída de tanques de armazenagem de matérias-primas, tanques de mistura, moinhos para dispersão de pigmentos no veículo, tanques de completagem e ajustes finais, além da unidade de enlatamento e embalagem.
A diferença entre a tinta e o verniz é a pigmentação, presente no primeiro e ausente no segundo. Temos ainda o esmalte, que é transparente como o verniz, mas apresenta coloração. Todos são usados com dois objetivos básicos: proteção e embelezamento. Codificação, sinalização, identificação e propaganda são aplicações secundárias das tintas e principalmente dos vernizes.
Você já se perguntou como a tinta se fixa na parede? A grande responsável é a resina termoplástica, produto obtido a partir do petróleo que compõe as tintas. Quando em contato com a superfície, ela se solidifica, formando uma película que se fixa à parede ou objeto pintado.
Além da formulação, o controle da qualidade de tintas também é feito por profissionais da Química e consiste na execução de ensaios físico-químicos para verificar abrasão (resistência ao atrito), aderência, brilho, viscosidade etc. Não é menos importante a participação desses profissionais no controle de emissões gasosas, tratamento de efluentes líquidos e resíduos sólidos das indústrias de tintas.
Para prevenir os acidentes e minimizar os riscos que eles trazem ao meio ambiente, à saúde da população e ao patrimônio público, o Brasil vem adotando uma legislação rigorosa em relação ao transporte de produtos químicos por via rodoviária. São decretos, leis, resoluções, portarias e normas editadas por órgãos como a ANTT, Conselho Nacional de Trânsito, Denatran, Ministério dos Transportes, Inmetro e ABNT.
Para poderem trafegar pelas estradas brasileiras, os caminhões que transportam produtos ou resíduos químicos perigosos são obrigados a adotar uma série de medidas de segurança.
O motorista precisa ser treinado para conduzir produtos perigosos. Na viagem ele tem que levar a documentação com dados sobre a classificação da carga, o fabricante ou importador do produto, as autorizações para circulação e informações de segurança para o caso de acontecer um acidente, além de um kit de emergência pronto para ser usado em caso de acidente.
O caminhão tem que estar em boas condições de manutenção e externamente precisa estar sinalizado com placas indicativas para mostrar o produto (ou produtos) que carrega e seus riscos. A indicação dos perigos é feita por painéis de segurança e rótulos de risco, que trazem números e símbolos indicando a classificação dos produtos transportados e seu enquadramento em uma das classes ou subclasses especificadas na Resolução da ANTT. Existem cerca de 3.500 números ONU relacionando os produtos perigosos. Os produtos químicos perigosos são divididos em 9 classes: 1-explosivos, 2-gases, 3-líquidos inflamáveis, 4-sólidos inflamáveis; substâncias sujeitas a combustão espontânea; substâncias que em contato com água emitem gases inflamáveis, 5-substâncias oxidantes e peróxidos orgânicos, 6-substâncias tóxicas e substâncias infectantes, 7-materiais radioativos, 8-substâncias corrosivas, 9-substâncias e artigos perigosos diversos. As classes podem ter subclasses como, por exemplo, os gases, subdivididos em três grupos: gases inflamáveis, gases não inflamáveis e não tóxicos e gases tóxicos.
Profissionais da química
O trabalho dos profissionais da química está presente em toda a cadeia de produção, distribuição, transporte e descarte de produtos químicos e resíduos classificados como perigosos, nas empresas de atendimento a emergências, nos órgãos públicos, nas universidades, nos laboratórios e nos transportadores.
Na área de transporte, por conhecer as propriedades e características dos produtos químicos, o profissional da química atua na orientação quanto à estocagem e quanto ao transporte propriamente dito, além de atuar na descontaminação dos tanques de carga e no tratamento de resíduos.
Os profissionais da química também atuam em campo, no trabalho de atendimento a emergências ocorridas durante o transporte de produtos perigosos. Eles são responsáveis pela identificação, neutralização e remoção de produtos derramados em consequência de acidentes, definindo quais as ações a serem tomadas para evitar danos à saúde da população e ao meio ambiente.
Em alguns casos, eles podem determinar a construção de diques, para evitar que poluentes atinjam cursos d?água e a canalização de água potável, evitando assim acidentes ambientais que poderiam adquirir grandes proporções.
Biodeterioração
As estruturas da celulose e da hemicelulose fazem com que a madeira seja o alimento de organismos extremamente ativos, os insetos e os fungos. Eles são os principais responsáveis pelo processo de biodeterioração desse material. Estes organismos são conhecidos como xilófagos – a denominação vem do grego, xylo-madeira, phagein-comer. Os xilófagos que causam os maiores prejuízos são os fungos, os cupins e as brocas-de-madeira, que podem provocar danos irreversíveis a residências, prédios, obras de arte e patrimônio histórico.
Os fungos causam bolor, manchas profundas, apodrecimento da madeira, e podem reduzir a resistência ao impacto e aumentar a permeabilidade em madeiras intensamente atacadas. Eles proliferam em áreas afetadas pela umidade, já que a água é essencial para o desenvolvimento desses organismos. Existem os fungos emboloradores, os manchadores e os apodrecedores que causam profundas alterações nas propriedades físicas e mecânicas da madeira porque vão destruindo gradativamente as moléculas das paredes celulares. Os fungos apodrecedores se subdividem em três grupos: fungos de podridão branca, que degradam todos os componentes químicos estruturais da madeira, incluindo a celulose, os de podridão parda, que atacam moléculas de celulose e de hemicelulose da madeira e os fungos de podridão mole que atacam a superfície da madeira.
Dentre os insetos xilófagos, os cupins e as brocas-de-madeira são os principais responsáveis pelos danos causados às madeiras. Eles pertencem a duas ordens diferentes de insetos: os cupins são da ordem dos isópteros, e as brocas da ordem dos coleópteros. Há milhares de espécies de brocas; algumas atacam as árvores vivas, outras espécies atacam as árvores recém-abatidas, quando a umidade da madeira ainda é elevada, um grupo ataca a madeira durante a secagem e outro ataca a madeira seca. Já os cupins também se subdividem entre grupos que formam colônias dentro da madeira seca e da madeira úmida e os cupins subterrâneos, entre outras categorias. Os que causam os maiores prejuízos a prédios e edificações são os cupins subterrâneos, que podem criar colônias em espaços não utilizados dos prédios.
Tratamento de preservação
Tratar a madeira com preservantes químicos antes de usá-la aumenta sua resistência aos ataques de organismos que causam a deterioração e garante sua durabilidade. Estes preservantes podem ser de três tipos: oleosos, derivados do alcatrão de hulha, oleossolúveis, que contêm misturas complexas de agentes fungicidas e/ou inseticidas e hidrossolúveis, produtos contendo misturas de sais metálicos.
A forma de aplicação do produto preservante pode ser sem ou com pressão. Os métodos sem pressão impregnam a madeira superficialmente e podem ser aplicados de três formas: por aspersão, com o uso de pulverizadores; por imersão, quando a madeira é imersa totalmente em um tanque que contém preservantes por alguns segundos ou minutos; ou por pincelamento do produto. O método de aplicação do preservante com pressão faz com que a madeira fique profundamente impregnada pela substância, e deve ser executado em uma autoclave, equipamento de grandes dimensões disponível em usinas de tratamento de madeiras.
Medidas curativas
Quando a madeira já está infestada por cupins ou brocas-de-madeira é preciso adotar medidas curativas para interromper a ação do organismo que está causando a deterioração. Para isso são usados produtos biocidas. Estes produtos são aplicados na forma de gases tóxicos, de pó ou de soluções inseticidas e fungicidas
A fumigação é um tratamento em que se usa um gás tóxico por tempo suficiente para atuar contra os insetos. O gás penetra profundamente na madeira e atinge os insetos em seu interior. Como o gás não possui ação residual, é necessário utilizar-se uma solução inseticida para evitar a reinfestação na peça.
O tratamento com solução inseticida contra cupins e brocas-de-madeira pode ser executado com seringa, pincelamento ou aspersão. Quando a solução é aplicada por injeção a impregnação é mais profunda. A injeção é aplicada através dos orifícios produzidos pelos insetos ou por pequenos orifícios auxiliares abertos com furadeiras. Para tratar partes de um prédio, como rodapés, batentes e guarnições de portas e janelas, por exemplo, são usados pulverizadores, que atingem áreas maiores. O tratamento com solução fungicida é indicado para a peça de madeira atacada por fungos apodrecedores.
A presença do químico é importante em todos os processos que envolvem tratamento de madeiras e aplicação dos produtos químicos, seja para prevenir a ocorrência, seja para eliminar insetos e fungos que já estejam instalados. O químico atua na formulação dos produtos que são utilizados nestes processos, e deve ser o responsável técnico nas empresas que atuam nesta área.
Sulfato de cobre, para conferir ação fungicida, dicromato de potássio ou de sódio, para ação fixadora, ácido bórico, responsável pela ação inseticida, e ácido acético glacial ou vinagre, por sua ação acidificante. Estes são os ingredientes indicados pela Coordenadoria de Assistência Integral da Secretaria de Agricultura e Abastecimento do Estado de São Paulo para a fabricação caseira de um produto indicado para o tratamento de madeira de eucalipto. Nada mais é do que uma fórmula química, que permite ao agricultor elaborar um tratamento preservante para a madeira que irá compor a cerca de sua propriedade, e mais uma comprovação de que a química está presente em diversas situações do nosso cotidiano.
As indústrias de galvanoplastia que atendem as indústrias metalúrgicas e da construção civil utilizam principalmente os metais cádmio, crômio, níquel, cobre, zinco e estanho para o revestimento das peças. A indústria de folheados reveste artigos de bijuteria e similares usando principalmente ouro, prata, ródio e paládio.
O processo
O processo de galvanoplastia é realizado em três etapas: pré-tratamento, tratamento e pós-tratamento das peças. O pré-tratamento consiste na preparação da superfície da peça para que tenha aderência, favorecendo também a uniformidade e a aparência do metal que será depositado. O pré-tratamento pode ser realizado por escovação, lixamento, polimento, decapagem e jateamento para remoção de rebarbas, sulcos, tintas, graxas e ferrugem. Na etapa de tratamento a peça é submetida a um ou mais banhos de metais para que adquira uma fina camada metálica. Nessa fase, a peça é ligada ao pólo negativo de uma fonte de corrente contínua tornando-se cátodo, no qual ocorre a deposição do metal. Para a cromeação, por exemplo, a peça passa por um banho de cobre, outro de níquel e ao final recebe uma camada de crômio. O pós-tratamento consiste em um processo de lavagem com água fria ou quente, secagem em centrífuga, estufa ou jatos de ar, banho de óleo para embalagem, proteção e pintura ou envernizamento.
Outros tratamentos de superfícies
A anodização é outro tipo de tratamento de superfície aplicado apenas para o alumínio. Trata-se de um processo de oxidação forçada, em que o alumínio e suas ligas são oxidados, formando uma camada protetora, isolante e com alta dureza. A anodização pode deixar a peça de alumínio com aparência brilhante, pode acrescentar uma série de cores mediante a utilização de pigmentos orgânicos ou inorgânicos ou produzir uma película espessa e dura, com alta resistência à abrasão. A peça anodizada também pode se tornar fosca ou ganhar propriedades contra a corrosão ou o desgaste.
O processo chamado de eletrodeposição faz a metalização em plástico. É uma aplicação decorativa ou funcional do metal sobre uma superfície plástica, que traz benefícios técnicos e estéticos. A eletrodeposição aumenta a resistência à corrosão em peças de automóveis, por exemplo. Este tipo de metalização tem a vantagem de produzir peças com pesos menores que as peças metálicas. A metalização em plásticos é usada em peças sanitárias que requerem camadas de alta duração e resistentes à água e à umidade, em geladeiras, máquinas de lavar, eletrodomésticos e em peças de acabamento para a indústria automobilística, como grades frontais e frisos externos dos veículos. Equipamentos eletrônicos também usam este tipo de acabamento. A eletrodeposição utiliza cobre, níquel, níquel acetinado e cromio. O resultado é um acabamento brilhante e acetinado, que pode ter uma série de cores, como dourado, prateado e vários tons metálicos.
Como em outras áreas da indústria, a nanotecnologia já começa a ser utilizada no setor de revestimento de superfícies. Partículas hidrofóbicas já estão sendo utilizadas no Japão nos banhos metálicos e nas tintas para evitar que a água se acumule nas superfícies. Esta tecnologia é usada na produção de peças para geladeiras, máquinas de lavar e fogões. A nanotecnologia também pode criar substitutos para substâncias perigosas usadas nos processos tradicionais da galvanoplastia, como o cromio hexavalente e os pigmentos anticorrosivos usados em pintura. Outra aplicação da nanotecnologia neste setor envolve produtos com maior resistência à corrosão.;
O papel do Químico
A presença dos profissionais da Química é de suma importância nas empresas que trabalham com tratamentos de superfícies, especialmente a galvanização. Pelos tipos de reagentes utilizados e pelas condições ambientais, as indústrias do setor de galvanoplastia estão entre as mais insalubres para os trabalhadores e as mais perigosas ao meio ambiente. Por lidar com banhos aquecidos, a vaporização é permanente, e a transferência de peças molhadas de um tanque a outro faz com que a chão esteja sempre molhado. Já no setor de polimento os trabalhadores lidam com muita poeira e ruído. Os sais dissolvidos nos banhos e os vapores liberados no ar podem causar problemas de saúde. Além disso, em consequência do processo de produção, as empresas geram grandes quantidades de efluentes líquidos, emissões atmosféricas e resíduos sólidos com alta carga tóxica, com metais pesados e, em alguns casos, com cianetos, que devem ser gerenciados e tratados de maneira adequada e consciente, atendendo às normas ambientais. Por isso, estas empresas precisam estar registradas nos Conselhos Regionais de Química e as operações devem ser conduzidas por profissionais da Química devidamente habilitados e registrados nos CRQs.
O trabalho dos químicos é importante em todas as etapas de produção do vidro. Os profissionais da química atuam no controle de qualidade das matérias primas, na formulação dos compostos, na condução do processo de fabricação do vidro e ao final do processo, no descarte de resíduos e efluentes, quando adotam procedimentos de forma a causar o menor impacto possível ao meio-ambiente.
Nem líquido, nem sólido
O vidro é uma substância inorgânica com características do estado líquido, mas que, quando resfriado, alcança um grau de viscosidade tão alto que se torna rígido para todos os usos práticos. Assim, visto sob o aspecto científico, o vidro é um líquido, mas com viscosidade tão elevada que, do ponto de vista prático, parece um “sólido”. Quando aquecemos o vidro ele se torna menos viscoso, ou seja, mais fluido, e por isso as peças de vidro são moldadas enquanto o material está fundido. A fusão de seus componentes, como o dióxido de silício, só acontece em uma temperatura muito alta, a 1.700°C, o que exige o consumo de muita energia. Para reduzir os custos de produção são acrescentadas à mistura óxidos metálicos, que reduzem o ponto de fusão da sílica até valores em torno de 800°C.
De acordo com a proporção de materiais secundários utilizados obtêm-se diferentes tipos de vidros, que podem ser divididos em três categorias:
- Sodo-cálcico: é o vidro comercial mais comum e o mais barato, e responde por 90% da produção. É usado principalmente em embalagens, como garrafas, potes e frascos, e também para produção de copos, vidro de janela, na indústria automobilística e em eletrodomésticos. Não resiste a altas temperaturas, a mudanças bruscas de temperatura, nem a produtos químicos corrosivos.
- Ao chumbo: leva uma alta percentagem de óxido de chumbo (20% a 30%) o que o torna um vidro de alta densidade e alto índice de refração. Tem uma superfície lisa e por isso é usado para fabricação de vidraria refinada, como cálices e taças, ornamentos e peças artesanais, já que o chumbo confere uma aparência mais brilhante ao material. Não resiste a altas temperaturas nem a mudanças súbitas de temperatura.
- Borossilicato: o terceiro maior grupo, é qualquer vidro que tenha pelo menos 5% de óxido de boro em sua composição. Ele tem maior resistência às mudanças térmicas e à corrosão química. É usado em processos químicos nas indústrias, em laboratórios, na indústria farmacêutica, em objetos ópticos e científicos e em lâmpadas de alta potência. Nos utensílios domésticos, é o vidro usado para fabricação de panelas e produtos resistentes ao calor.
Em relação aos usos, o vidro pode ser dividido em quatro tipos:
Vidros para embalagem, usados para embalar bebidas, medicamentos e produtos cosméticos;
Vidros domésticos, que incluem copos, xícaras, travessas, vasos e objetos de decoração;
Vidros planos, fabricados em chapas, e usados em janelas, portas, espelhos, na indústria automobilística, móveis e em eletrodomésticos como geladeiras e microondas;
Vidros especiais, com usos específicos, como os vidros usados em bulbos de lâmpadas, garrafas térmicas, fibras óticas e blocos isoladores.
Fabricação
As principais matérias-primas para produção de vidro são areia (sílica), feldspato, calcário, carbonato de sódio, carvão, sulfato de sódio, hematita e sucata de vidro. A areia utilizada na manufatura do vidro deve ser quase quartzo puro, mas apesar de ser abundante na natureza, ela precisa ter determinadas características mineralógicas, químicas e granulométricas para ser usada. A barrilha – Na2CO3 – entra na composição do vidro porque contribui para reduzir a temperatura de fusão da areia. Outros componentes são o óxido de chumbo, carbonatos e outros sais necessários para colorir o vidro. Nas operações de acabamento, usam-se diversos produtos, como abrasivos e ácido fluorídrico.
As etapas de produção incluem o transporte das matérias-primas para a fábrica; a classificação dos materiais; a pesagem, a mistura das matérias-primas e a introdução da massa no forno. Os procedimentos de fabricação passam por quatro etapas principais: fusão, conformação ou moldagem, recozimento e acabamento. No forno o vidro é fundido e passa para a etapa de conformação ou moldagem, quando uma máquina molda o objeto em poucos segundos, muitas vezes usando o ar. Toda a operação é feita em tempo relativamente curto, porque o vidro transforma-se rapidamente de líquido viscoso em “sólido”.
Os tipos de vidro mais comuns conformados mecanicamente são os vidros de janelas, as chapas de vidro, as garrafas, os bulbos de lâmpadas e os tubos. Após adquirirem seu formato final os objetos passam por recozimento, que é um tratamento térmico, e resfriamento. Depois são submetidos a inspeção e transformação, caso sejam decorados, até chegar à etapa de embalagem. Todas as etapas de produção nas modernas fábricas de vidro são feitas em máquinas automatizadas, em movimento contínuo.
Como as características físicas e químicas das matérias-primas é que determinam a qualidade e as especificações do vidro a ser produzido, o trabalho dos químicos é importante porque as matérias primas devem ser analisadas e suas especificações devem ajustar-se às exigências de produção de cada tipo de vidro.
Evolução
Técnicas de fabricação antigas, da época de assírios e fenícios, e hoje perdidas, utilizavam cera e moldes de argila para produzir objetos de vidro. O grande passo no processo de manufatura se deu com a invenção do tubo para soprar vidro, surgido em torno de 250 a.C. Nesta técnica utiliza-se um tubo de ferro com cerca de 1,5 metro de comprimento dotado, de um lado, de um bocal, e de outro, de uma pequena dilatação. Nesta parte dilatada coloca-se uma pequena massa de vidro fundido, que, ao ser soprada forma um balão. Rodando o balão é possível modelá-lo com uma ferramenta de ferro, dando-lhe as mais variadas formas. Esta é uma técnica milenar que permanece inalterada até dias de hoje, e é usada por artesãos na fabricação de peças artísticas e requintadas.
Foi a fabricação dos vidros planos que passou pelos maiores avanços ao longo do tempo. A produção era manual até o início do século XX, quando o vidro era aberto da mesma forma que a massa, com um rolo. Em 1914 foi criado na Bélgica o processo Fourcault de fabricação contínua de folha de vidro. Hoje a produção de vidro plano é realizada pelo método float, inventado em 1959 na Inglaterra. O vidro fundido é colocado em uma piscina sobre metal fundido, em atmosfera controlada, em temperaturas entre 1100°C e 600°C, em que se dá o enrijecimento. Máquinas controlam a espessura do produto e ao final uma fita de vidro é obtida por laminação. Os fornos usados neste processo são geralmente do tipo contínuo; o material de fusão é carregado de um lado e o vidro fundido sai continuamente pelo outro lado, através de uma fenda. Rolos na saída fazem a laminação e alisam o material até formar as chapas. Grandes máquinas têm capacidade para produzir até 250 m² de lâminas por hora.
Reciclagem
O vidro não se decompõe na natureza e pode permanecer sob o solo por milhares de anos sem apresentar alterações, por isso sua reciclagem é tão importante. Além de reduzir o volume de detritos nos aterros sanitários, o uso de cacos de vidro na indústria reduz significativamente os custos de produção, porque diminui a necessidade de uso de matérias-primas virgens e porque a temperatura de fusão do vidro reciclado é mais baixa, o que demanda menos energia.
Para ser reciclado o vidro passa por uma central de triagem, onde é separado, triturado e transformado em pequenos cacos. Partes metálicas e impurezas são retiradas, e os cacos são lavados antes de serem reutilizados. Normalmente as fábricas adicionam à mistura das matérias-primas cacos de vidro gerados internamente, na própria fábrica, ou comprados de cooperativas ou outras empresas. Os cacos podem representar de 35% a 50% do total da mistura. O vidro reciclado pode ser utilizado inúmeras vezes, com o mesmo desempenho e qualidade do vidro produzido com matérias-primas virgens.